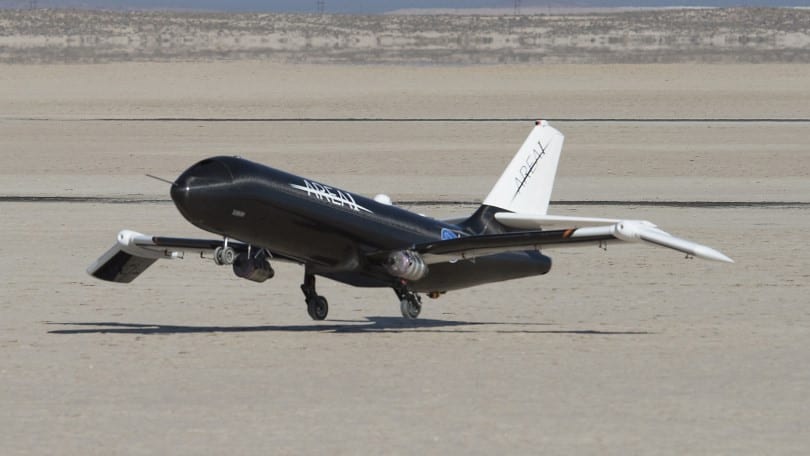
News
Flexible Alloy Wings For Supersonic Drones Tested by NASA and Boeing
Flexible Alloy Wings For Supersonic Drones Tested by NASA and Boeing
NASA and Boeing have announced this week the successful testing of a drone that will allow supersonic flight due to the development of an innovative material that allows its wings to dynamically change shape and position based on flight needs. This drone was successfully designed and tested as a result of collaborative work by carried out at NASA’s Armstrong Flight Research Center in California. Part of the Spanwise Adaptive Wing project, or SAW, the project aims to validate the use of a cutting-edge, lightweight material to be able to fold the outer portions of aircraft wings and their control surfaces to optimal angles in flight.
The project has tackled this problem by creating a very light alloy while maintaining its durability, known as Shape Memory alloy. Since this alloy is so light, it can be placed anywhere on the plane. This concept has been around for almost a century, but these new capabilities are definitely ground-breaking. A significant and unique property of the alloy is that it can be deformed and reshaped at room temperature – then, once heated up, it can return to its original position. The alloy material changes ‘phase’ at a very specific temperature, which means that there is no need for heating or cooling the actuators in order to allow it to respond. The extreme durability of Shape Memory alloy means the wing can endure considerable stress and still return to its original shape. NASA’s drone was able to shift its wingtips from 0 degrees to 0 degrees in its successful flight tests.
Though the principle of reducing drag on a plane might not be novel, but this new design shows a significant improvement in overall performance for flights of this type. Jim Mabe, a researcher at Boeing, said: “From the time we started initial testing here at Boeing, up to the flight tests, the material behaved consistently stable, and showed a superior performance to previous materials.”
The Shape Memory alloy was moulded into an actuator, allowing the wings to change shape mid-flight to properly adjust for wind and speed conditions. Because the module used to change the temperature of the alloy is significantly lighter and smaller than conventional frames and motors, the design is more compact than current drones. It addresses a long standing concern of flight design – weight has ‘weighed down’ on the minds of aircraft designers since the Wright Brothers. The use of actuators allows engineers to replace what would otherwise be bulky and heavy steel machinery, significantly reducing the overall weight of the craft. According to NASA, crafts with this material may weigh up to 80% less than the regular crafts that exist on the scene currently.
The development of super light materials makes way for impressive new designs and implies a future of aircrafts that will be able to go more places and offer higher controllability in the air. This development allows for smaller aircraft to reach supersonic speeds, and could also have an impact on the design of larger subsonic aircraft too; lighter aircraft are more fuel efficient, and more moving parts means higher airborne efficiency.
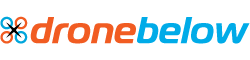