News
Drones as Part of Multi-Moment Analysis
There is extensive literature about drones in a logistics context, and numerous applications have been implemented, but there is one unique use case that hasn’t gotten momentum so far, yet offers significant potential. A paper published in the IOP Conference Series: Materials Science and Engineering journal focuses on this massive opportunity to deploy drones and support the monitoring of intra logistical processes such as Multi Moment Analysis (MMA).
This paper research efforts at the Budapest University of Technology and Economics, focusing on a special use case for drones in a manufacturing context. The main aim of the paper is to observe and measure the manufacturing process – and automate them to a large extent – resulting in faster, more reliable and cheaper systems which will offer benefits to both the logistics companies (performing the MMA) as well as the customer.
Describing the Architecture of a System Needed to Perform MMAs Using Drones
The authors begin describing the architecture of the system needed to perform MMAs using drones. They specifically focus on two key components: the indoor localization sub-system as well as the real-time closed-loop control algorithm which allows the drone to track the monitored object.
“Multi Moment Analysis is a measurement, where objects serving in the production supply processes, such as people, forklifts, etc. are observed with the intention of determining their utilization. During the measurement people walk around with clipboards and printed out forms, and at random times observe a certain object writing down what activity it was performing at the moment,” the authors stated while describing the MMA method.
The authors continue by evaluating their needs to design a system that is capable to monitor the objects that take part in production supply processes in a specified area with the help of drones. As they say, there are three main categories for the static architecture system.
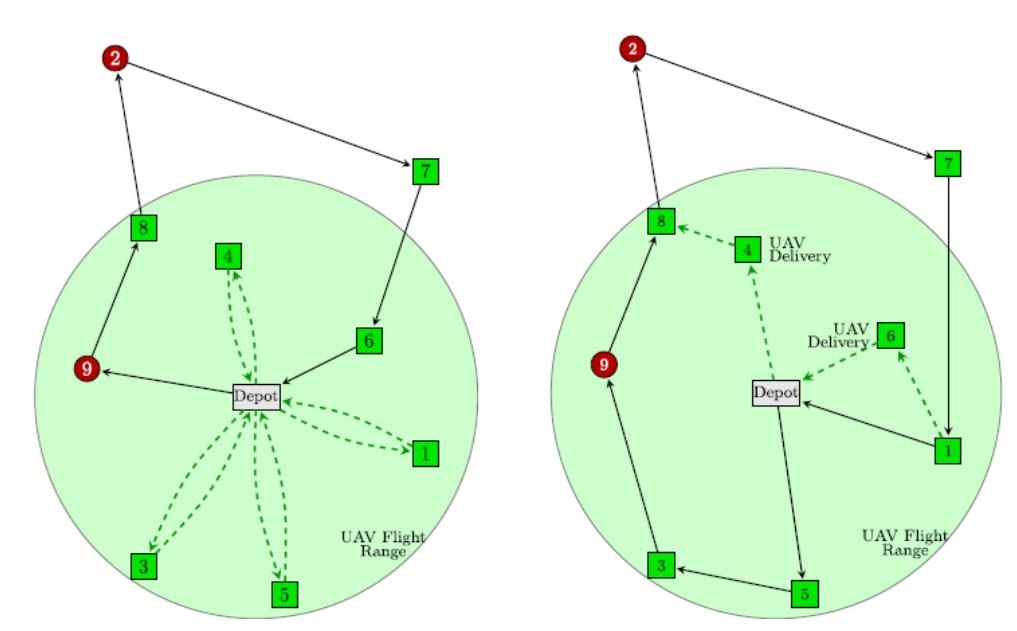
Parallel Drone Scheduling Travelling Salesman Problem (PDSTSP) and Flying Sidekick Travelling Salesman Problem (FSTSP)
The first is the observed airspace, the second is the observer airspace and the third is the IT & HR processes. In that manner, they construct and validate the algorithm which allows them to perform experiments with different scenarios.
After performing two sets of experiments, the authors found that this algorithm is viable and performs to their expectations. They stated:
“It is apparent that the drone (orange, starting from 0,0), finds the object (blue), follows it for a specified period of time with just a few hiccups, and then returns home. Using an arched path was important because it demonstrates that the algorithm does not get confused from an object that constantly is changing its direction.”
Future Objectives
In the future, the authors believe that this algorithm can be scaled and implemented in the control options of the drones, assuming an ideal physical environment with no obstacles. The next step would be to install a localization system, process the data that it transfers and control the drone based on that.
Some of the crucial challenges are centralized in the problem of assignment – a VRP problem with customers constantly in motion – as well as image recognition which could be done in a hybrid way. A step further, according to them, would be to recognize and record the activity of the object using purely image recognition and with that reducing the required human manpower while improving speed and reliability.
In the end, the authors conclude that the utilizing UAVs in assisting the MMA measurement is a unique research topic that “holds significant practical value that appears to be realizable in the rather near future.” As such, they are confident that the measurements can be made cheaper, faster and more reliable at the same time.
Citation: Monitoring of Production Line Supply Systems With Drones, B Mészáros, K Bóna and M Bertalan, IOP Conference Series: Materials Science and Engineering, Volume 448, Number 1, http://stacks.iop.org/1757-899X/448/i=1/a=012037
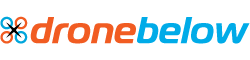